Co-Authored by Kieran Blacknall, Operations Manager and Cameron Russell, Laboratory Technician at Drytac.
When it comes to selecting the right adhesive for your sticking needs, it is easy to get caught up in the numbers. One common misconception is that higher tack equates to better adhesive performance and strength. However, the reality is far more complex.
Adhesive performance is determined by a combination of factors including tack, peel strength, shear strength, cohesion and adhesion. Each of these plays a crucial role in the overall effectiveness of an adhesive.
Tack
Starting with tack; this is often the first property that comes to mind when evaluating adhesives. It refers to an adhesive’s ability to form a bond of measurable strength immediately after contact with a substrate under low pressure. Tack may provide an initial stickiness but does not guarantee long-term performance.
In terms of solutions classed as ‘high tack,’ these adhesives may fail under stress or environmental changes. A high tack adhesive is ideal for situations where minimal pressure is required to create a bond, such as when applying a fragile glass mirror to a surface, or when you need a strong initial bond that can later be peeled from the substrate easily. This would fall into the high tack removable adhesive category.
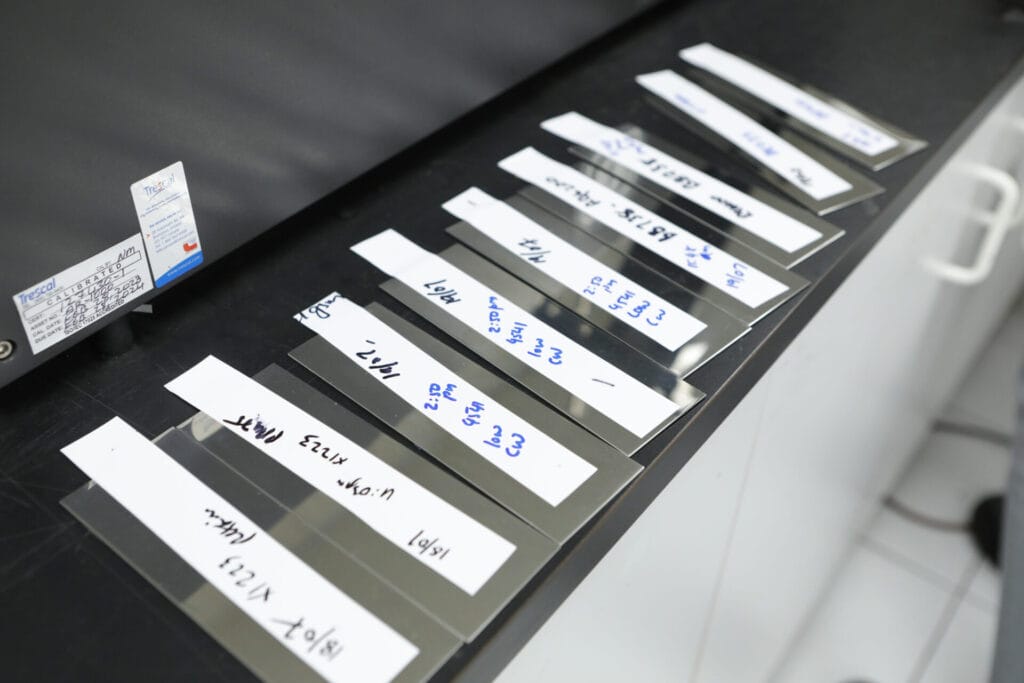
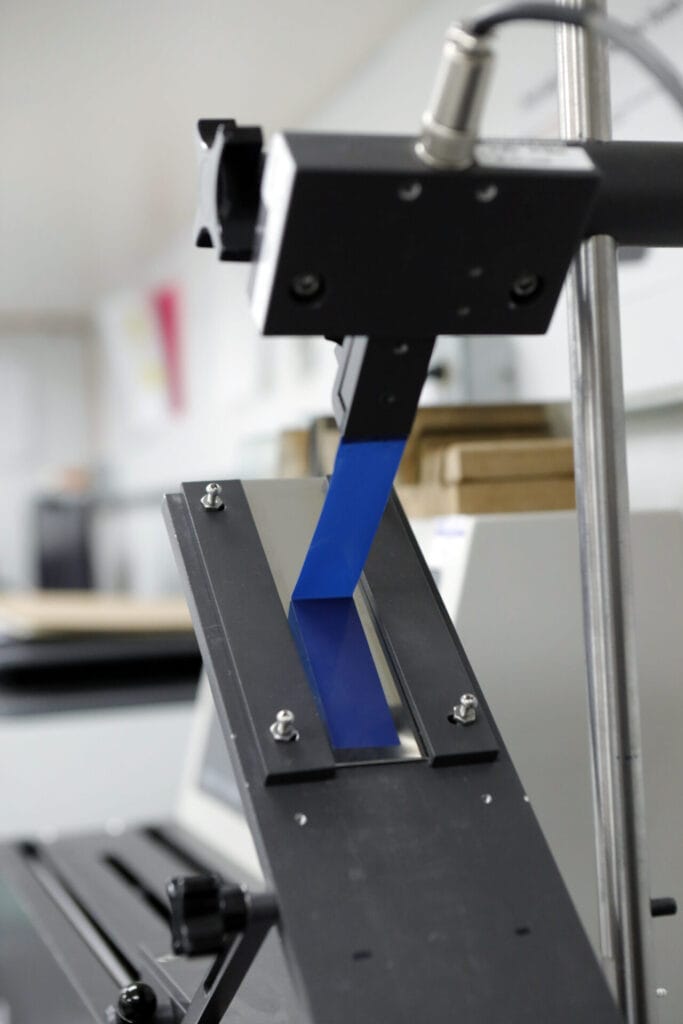
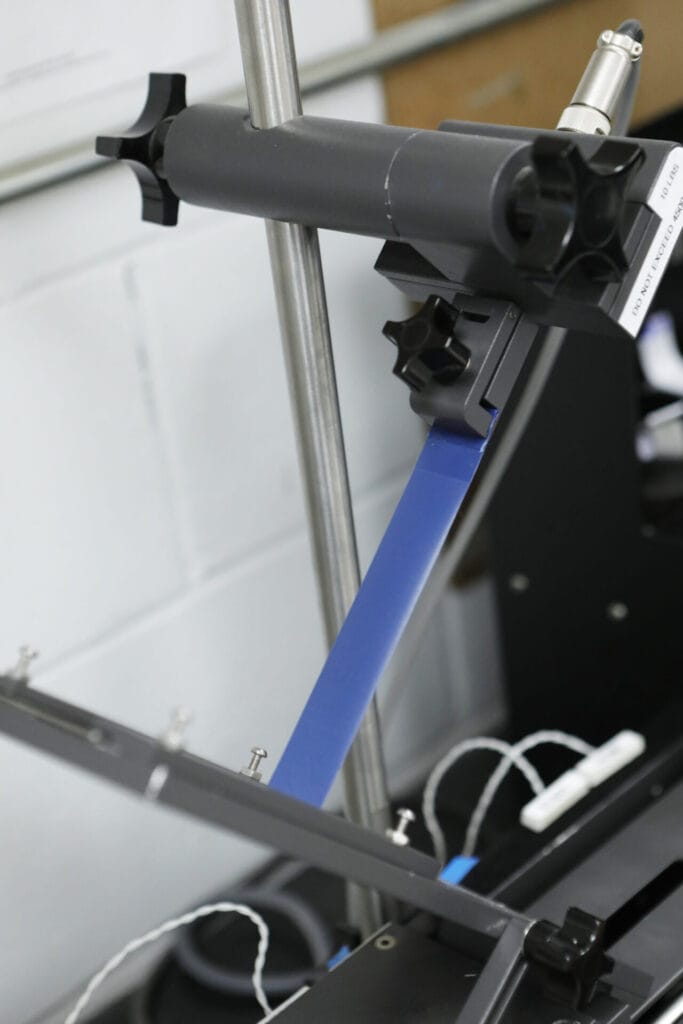
Peel Strength
Next up is peel strength, which measures the force required to separate two bonded materials by peeling one away from the other. The industry standard for this is 180/90 degrees for 20-25mm/min from stainless steel or glass. This property is crucial for applications where the adhesive must resist peeling forces such as in labels, tapes and protective films.
Peel strength is typically measured by applying a constant rate of peel to the bonded materials and recording the force required to separate them, with this measured in Newtons per metre. High peel strength indicates the adhesive can maintain its bond under peeling forces, which is essential for ensuring both the durability and reliability of the adhesive in real-world applications. Pressure-sensitive adhesives, also known as PSAs, are great for peel strength.
Shear Strength
Also up for consideration is shear strength, which refers to the adhesive’s ability to resist forces that cause the bonded materials to slide past each other. This is particularly important for structural applications where the adhesive must withstand significant loads over time, with 1kg being the standard weight for samples measuring 10cm x 10cm.
In terms of measuring shear strength, this is done by applying a force parallel to the adhesive bond until failure occurs. High shear strength – measured in time or converted Megapascals (Mpa) – helps ensure the adhesive can maintain its integrity under shear forces, making it suitable for applications such as mounting tapes and construction adhesives.
Also keep in mind that grams per square metre, or GSM, will make a big difference to shear strength. More adhesive tends to last longer as it continues to wet over time.
Cohesion
Professionals also need to consider cohesion, or the internal strength of the adhesive, which is determined by the interactions between the adhesive molecules. This is essential for maintaining an adhesive’s structural integrity and preventing it from breaking down under stress.
It’s also worth keeping in mind that cohesion is influenced by the chemical composition and molecular structure of the adhesive, as well as the curing process. High cohesion ensures the adhesive can withstand internal stresses and maintain performance over time, making it suitable for demanding applications where durability is critical.
Cohesive failure can occur when there is a breakdown in the structure of the adhesive, which in turn may leave behind adhesive on the substrate and on the carrier.
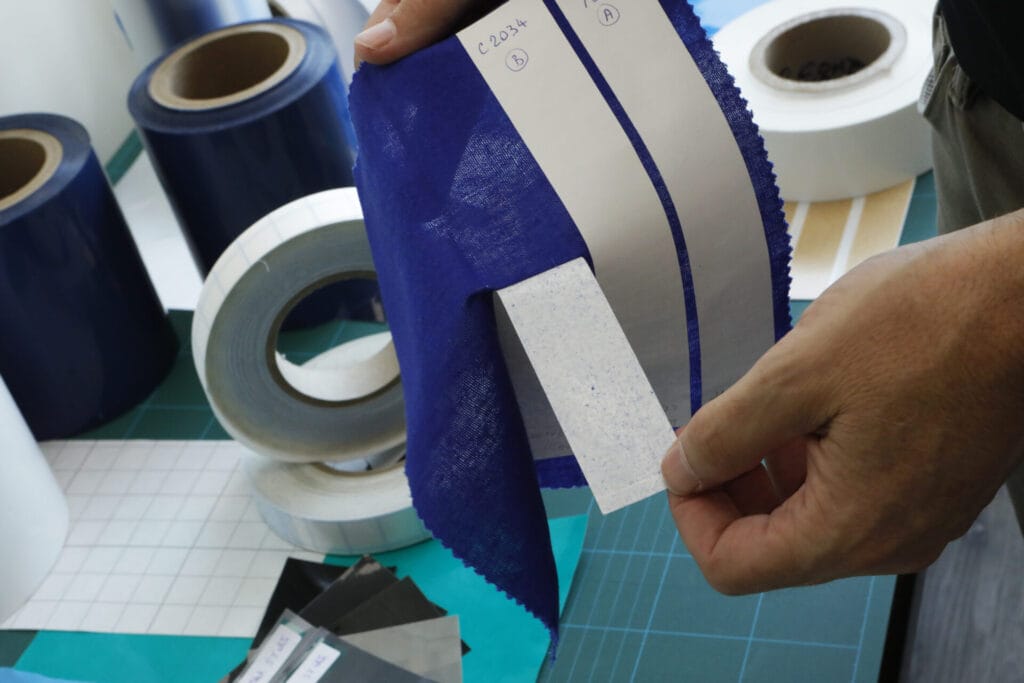
Adhesion
Finally, adhesion is the bond strength between the adhesive and the substrate. This is crucial for ensuring the adhesive can form a strong and durable bond with the materials it is intended to join.
Adhesion can be influenced by factors such as surface energy, surface preparation, and the chemical compatibility between the adhesive and the substrate. High adhesion ensures the adhesive can maintain its bond under various conditions, making it suitable for all manner of applications, ranging from automotive to medical to industrial uses.
You may encounter adhesive failure when there is a complete breakdown, or detachment, from either the substrate or the carrier.
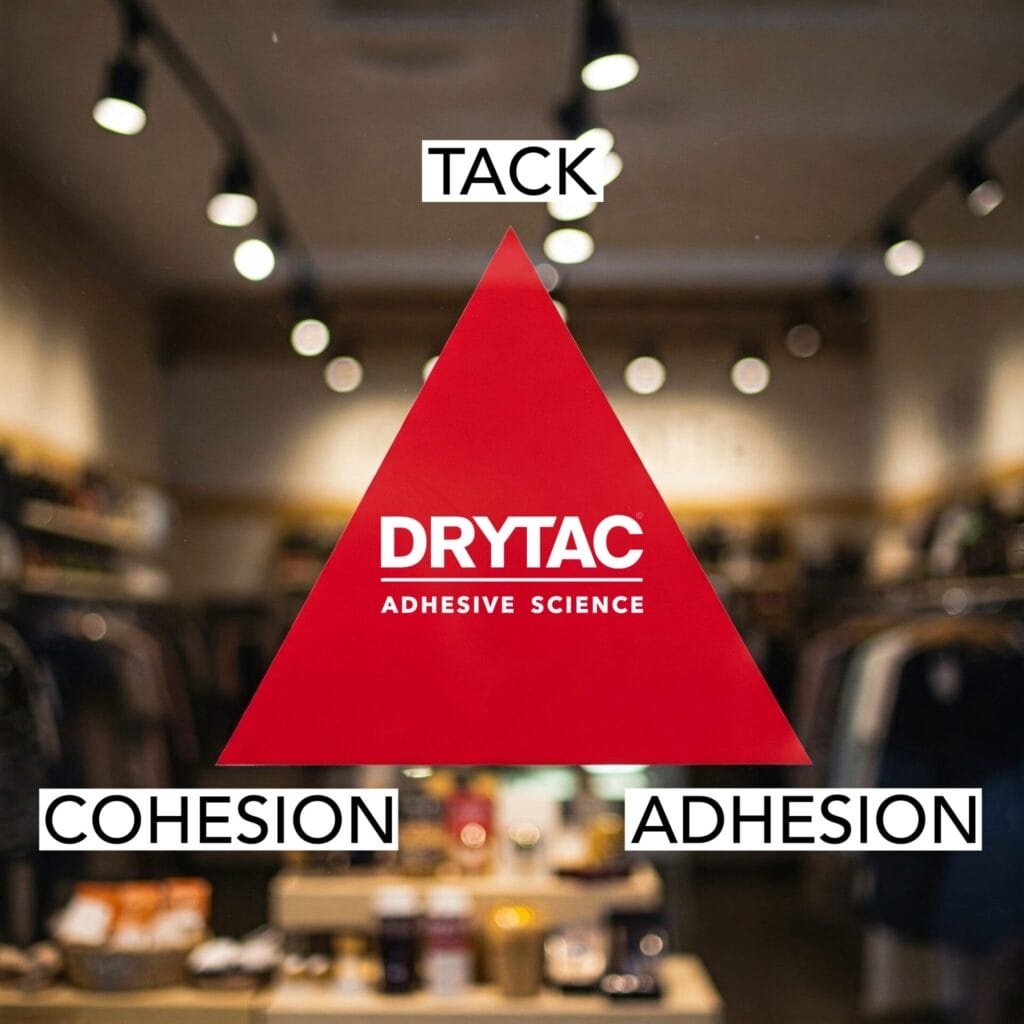
The Adhesion Triangle
To understand adhesive performance better, it is essential to consider something referred to as the ‘adhesion triangle’, which illustrates the relationship between tack, adhesion, and cohesion. A balanced adhesive formulation ensures all three work together to provide optimal performance.
Also remember each application requires different adhesive properties. For example, automotive adhesives need high shear strength, while medical adhesives require gentle adhesion. Testing methods specific to tack, such as the loop tack test, provide valuable insights to the laboratory but should not be the sole measure of adhesive performance.
Environmental factors such as temperature and humidity can significantly impact performance, with high humidity having the potential to reduce adhesion strength. However, plasticizers can be added to help with flexibility and migrate to adhesives, with this being accelerated in high temperatures and exposure to UV light. Also on the same subject, low temperatures can make adhesives brittle, so be wary of this when working with adhesive products.
Ultimately, the true measure of an adhesive’s quality lies in its real-world performance. Practical testing and application-specific evaluations provide a more accurate assessment than relying solely on laboratory test results.
By testing adhesives in real-world conditions, you can make more informed decisions and select the best adhesive for your specific needs.